Da ich mich damals für die C-Beam entschieden hatte aber nur mäßig zufrieden war mit den Ergebnissen in Aluminium, habe ich versucht das ganze iterativ an ein gutes Fräsbild hochzumodden und habe erst dann begonnen Komfortfunktionen nachzurüsten.
Stufenweiser Umbau der Führungen
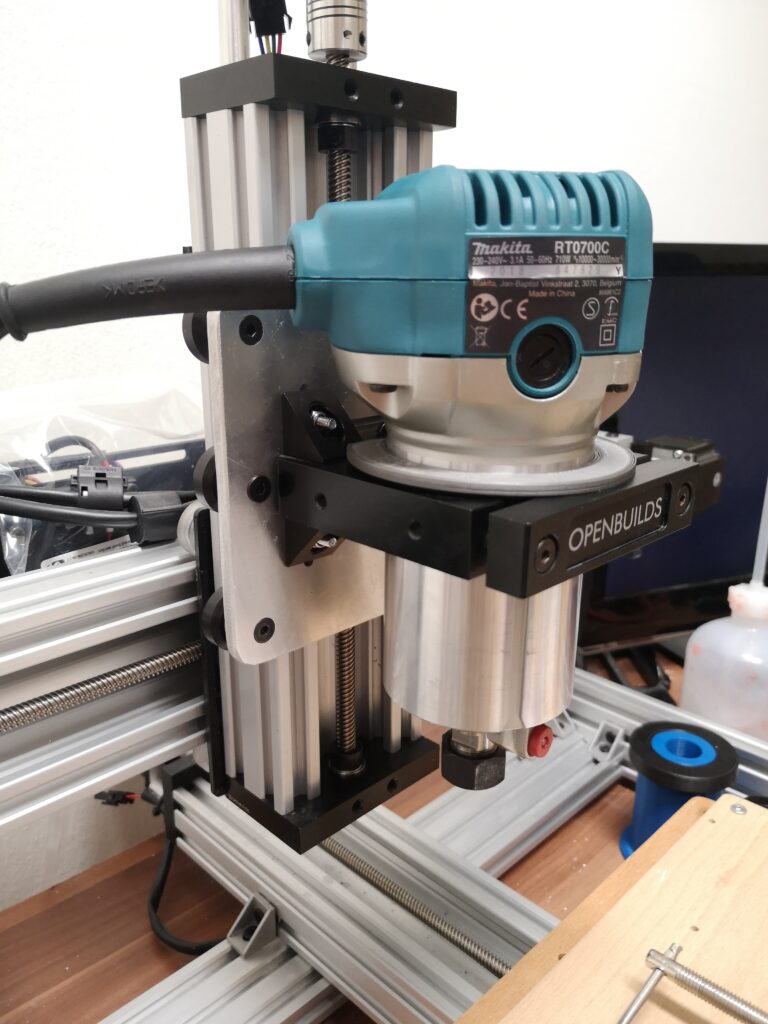
Im Original sind kleinere Rollen im inneren verbaut. Das macht es schwierig die Rollen einzustellen und auch der Ansatzpunkt ist viel schmaler und die Spindel hat es einfacher diese zu verwinden. Daher die Verlagerung der Rollen nach außen und Ergänzung um zwei weitere. Die Platte dafür habe ich auf der MPCNC fräsen können mit vorsichtigen Schnittwerten. (Einzahn Sorotec alu Fräser, ca 200-400mm/min, 1,5 doc volleingriff, ungekühlt@30000rpm)
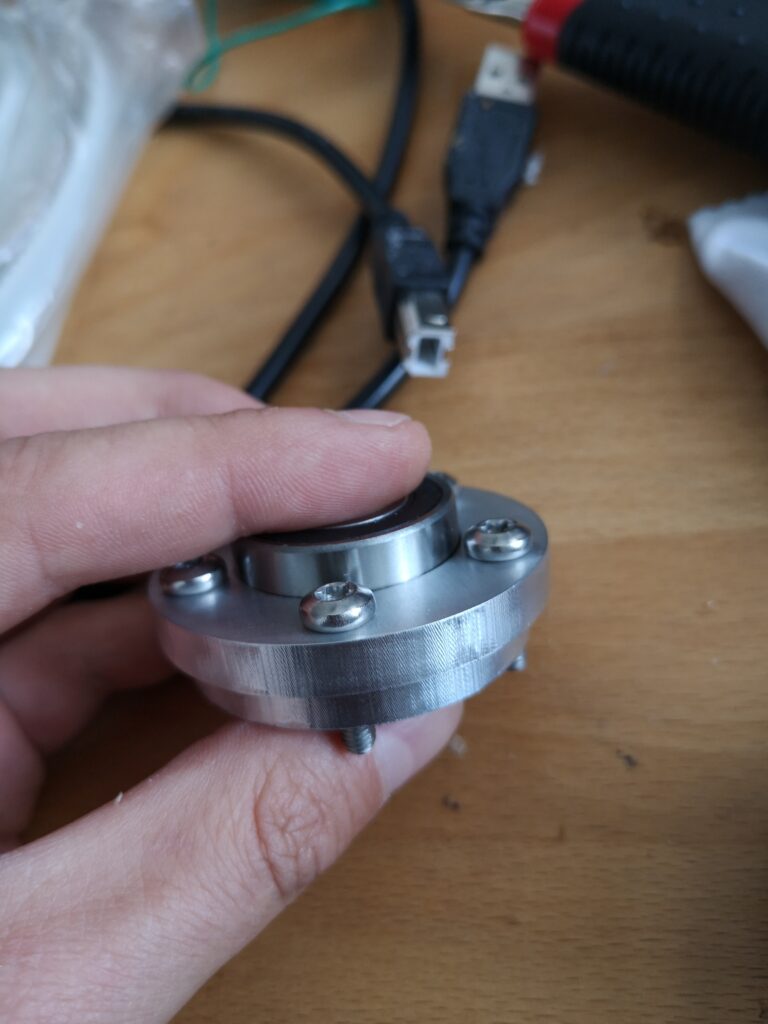
Danach war das Fräsbild etwas verfeinert also die flanken waren noch nicht „spiegelnd“ aber immerhin konnte ich einfache Teile fertigen.
Im nächsten Schritt habe ich dann doch auf Profilschienen umgerüstet. Es war stark zu überlegen ob das investieren in die Maschine lohnte aber zu dem Zeitpunkt gab es nicht viele Optionen. Da die Führungen relativ günstig waren und der Umbau fast ein Drop in Replacement, hab ich es dann riskiert. Die Halte und Verbindungsplatten sowie die Grundplatte kontn eich ohne Zwischenfälle auf der Vorgängerversion herstellen. Dies beschränkte sich ohnehin auf die Bohrungen (Bohrfräsen mit 3mm Fräser).
Die untere Platte neigt natürlich ein wenig sich zu verformen wenn man am äußersten punkt Kraft anbringt jedoch wollt ich mir die beiden zusätzlichen Extrusionen erstmal ersparen da ohnehin nicht viel Kraft in der Z-Achse zu erwarten war.
In dem Zuge habe ich auch gleich ein Gehäuse aus OSB Platten gemacht Hauptsächlich zur Lärmreduzierung aber auch um die Späne zu kontrollieren. Die Platten kamen von meinem Nachbarn und waren Verschnittreste aus einem Podestbau. Danke Stefan! Das ganze wurde später noch foliert um es haltbarer und optisch ansprechender zu machen.
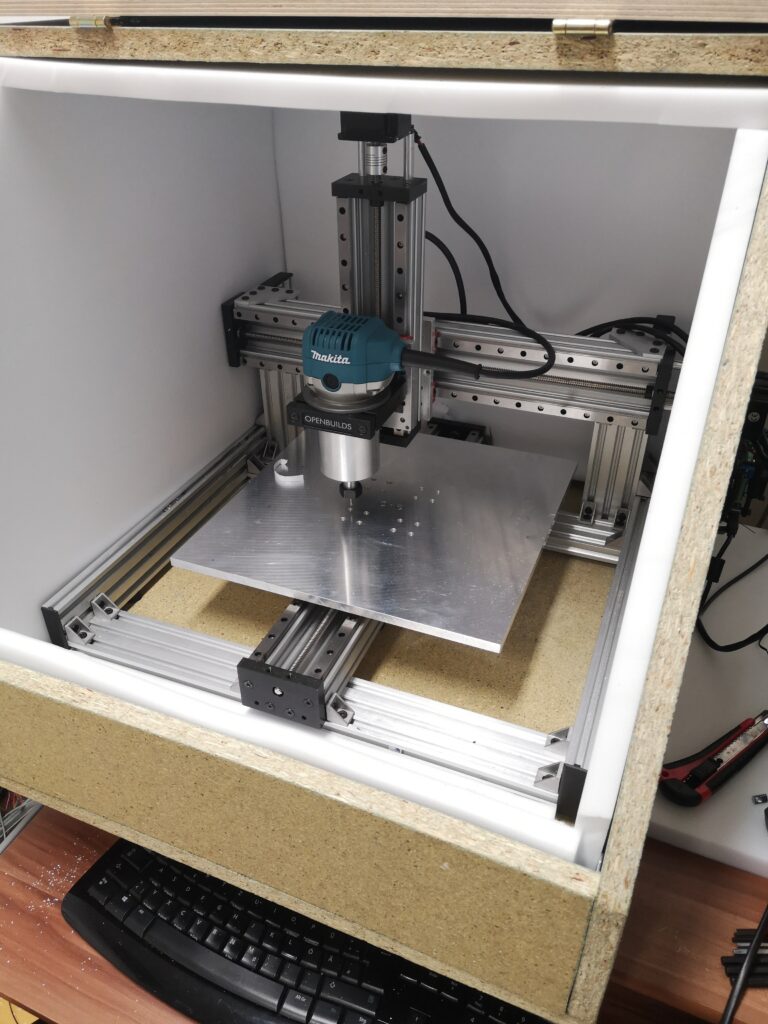
Das Fräsbild verbesserte sich glücklicherweise dramatisch, nach dem die ganze Maschine auch wieder neu ausgerichtet war.
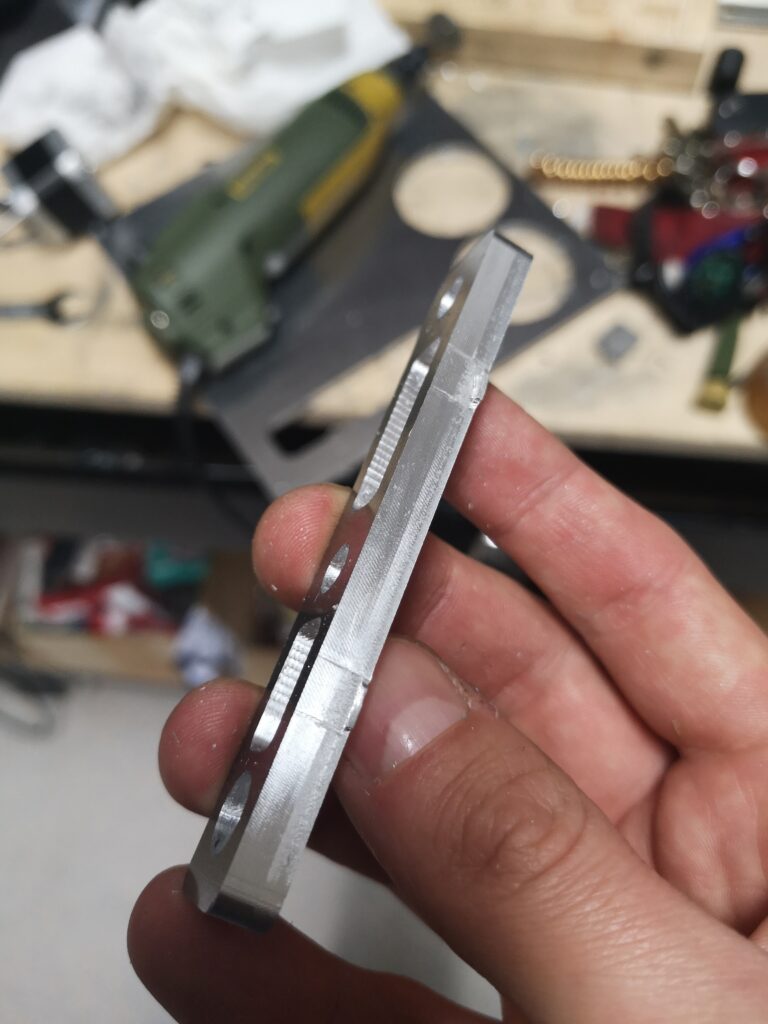
Das sah dann shcon ganz passabel aus trotz fehlender Kühlung und nur Spanevakuierung durch das Makitagebläse. Innen sieht man einen Adaptive Werkzeugpfad ohne anschließenden Schlichtungspfad.
Umbau der Elektronik
Original kommt nur eine Art Halteplatte für den Xpro CNC V3 von Sparkfun electronics im Ooznest kit mit. Das reicht grundsätzlich um die Maschine in Betrieb zu nehmen. Für so eine kleine Platine plus Netzteil lohnt auch keine Schaltschrank oder irgendwas, wie ich fand.
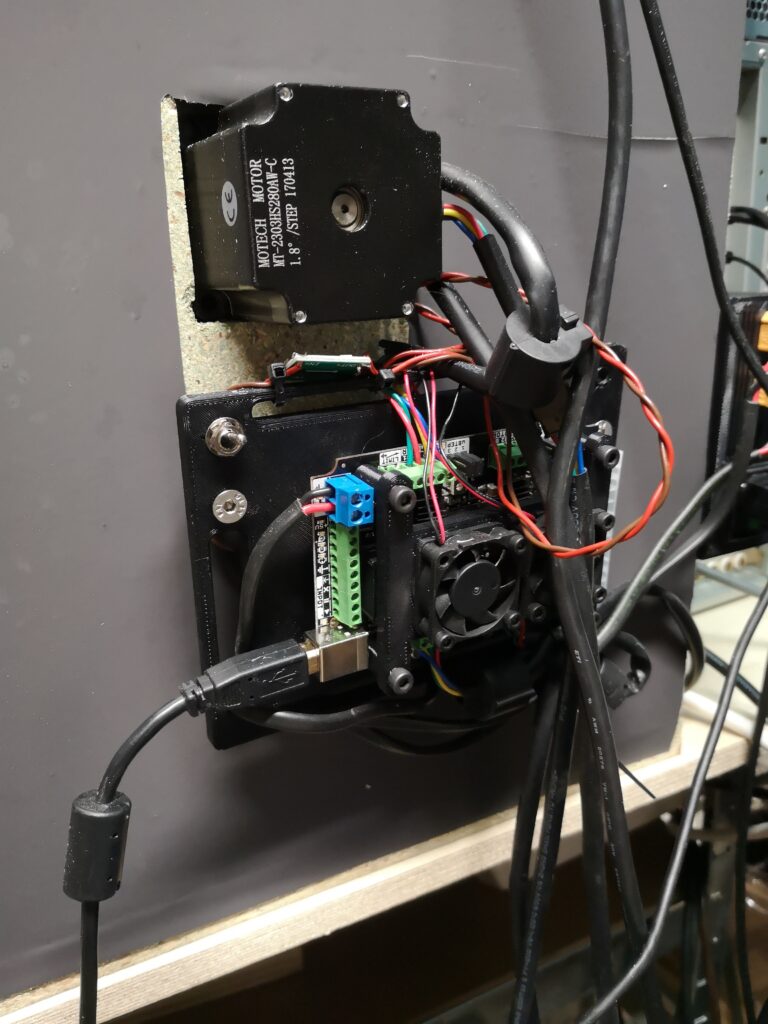
Daher habe ich das ganze ein 3D- gedrucktes Gehäuse https://www.thingiverse.com/thing:4583595 integriert mit einer Reihe beleuchteter Taster.
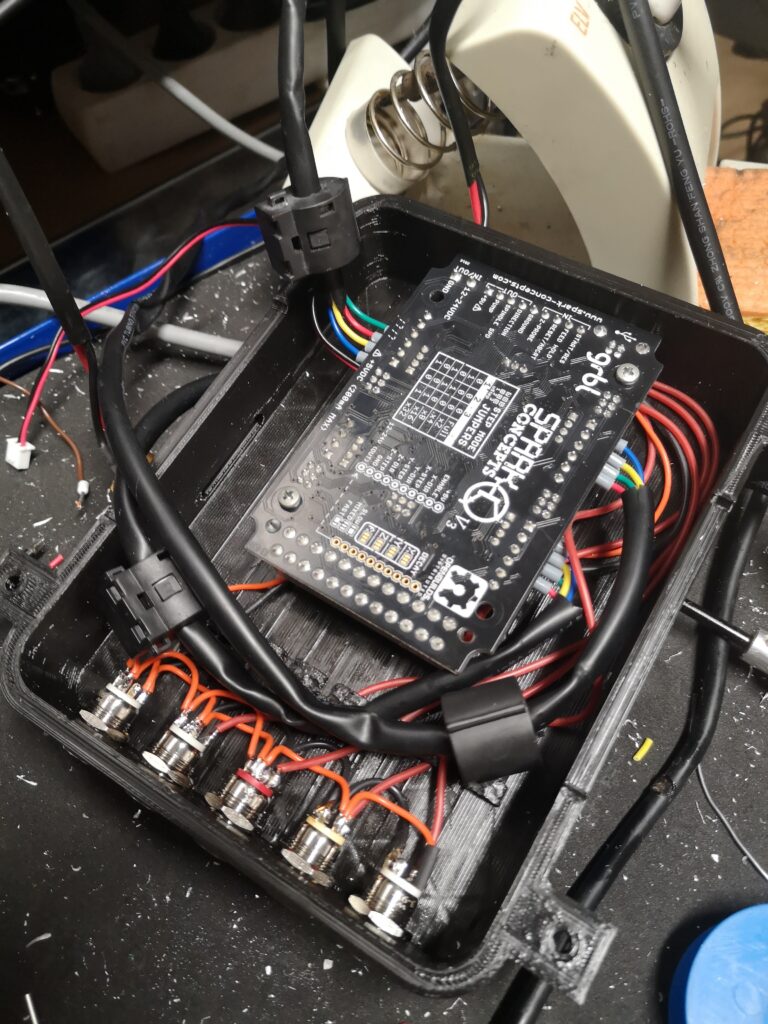
Das ganze wurde dann angeschraubt und ermöglicht jetzt, Start / Pause /Reset / Kühlung / Spindel An/Aus, wenn alles fertig ist. Es fehlt noch eine kleine FlipFlop Schaltung die das Relais hält wenn ich einzeln Taste. Die Schrittmotorentreiber sind gut gekühlt und die Kabel zugentlastet etc. Die restlichen Kabel müssen noch ordentlich verlegt werden natürlich.
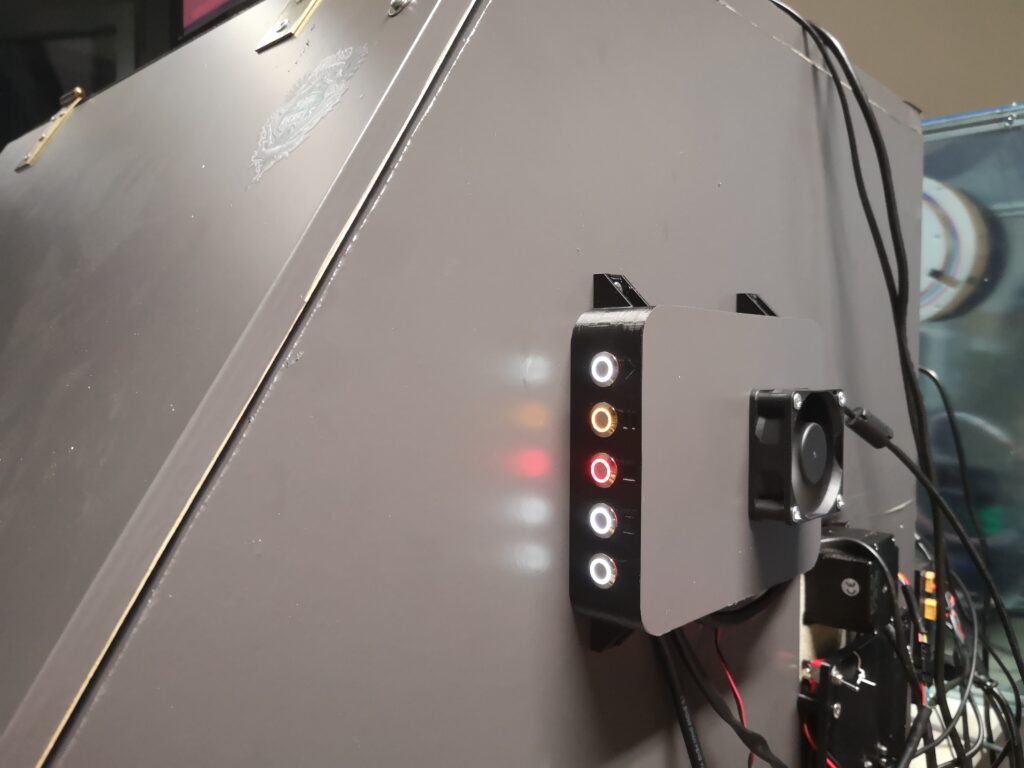