It has been a while since the last post and the reason for that is the design and manufacturing of a desk lamp. The initial design differs from the final product as the whole process has been simplified a little. I gathered materials for three of them so the first one will serve as a production test to find out if everything fits. Once finished I am going to include the finer details.

The pedestal is a 3D cnc piece made from walnut here. It has been changed to a more simple round apple wood base with a 10mm phase cut with a bandsaw. Since the apple wood has a real nice grain I like it even more by now. I made three of them and one is probably going to be machined on a lathe by a friend to get closer to the intended design.
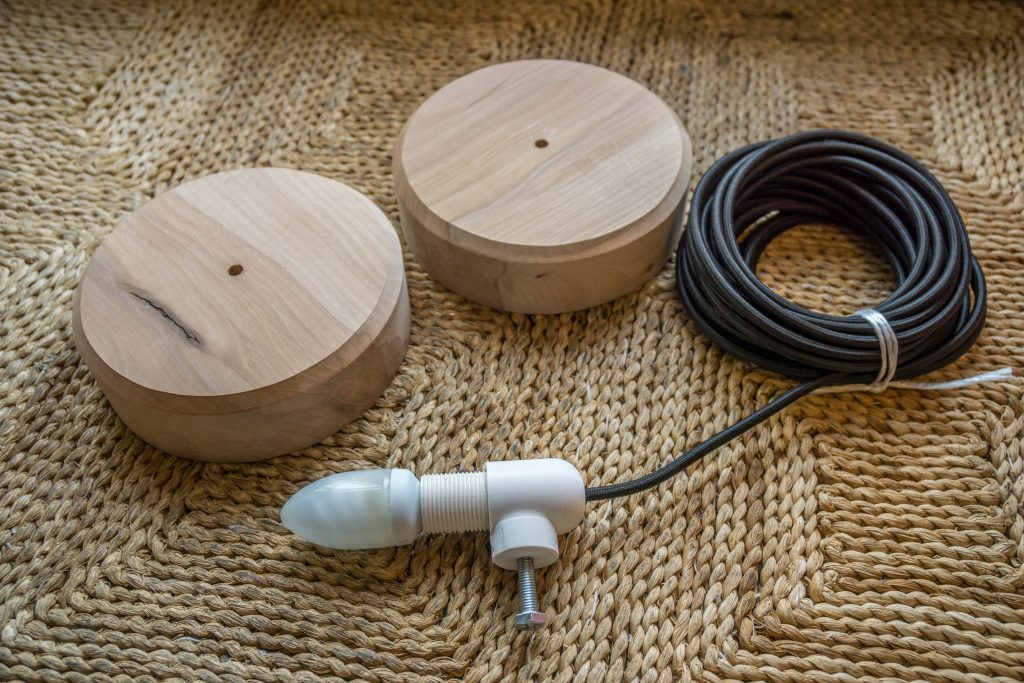
The switch case mounted in front is going to be replaced by an inline switch, this also eases up the amount of needed prints. The joint for the arms above has been redesigned and is now clamping instead of a bolt through design with three possible positions. I have not tested yet if the clamp produces enough force to hold the arms and the lampshade with all the components. I hope this works out well.
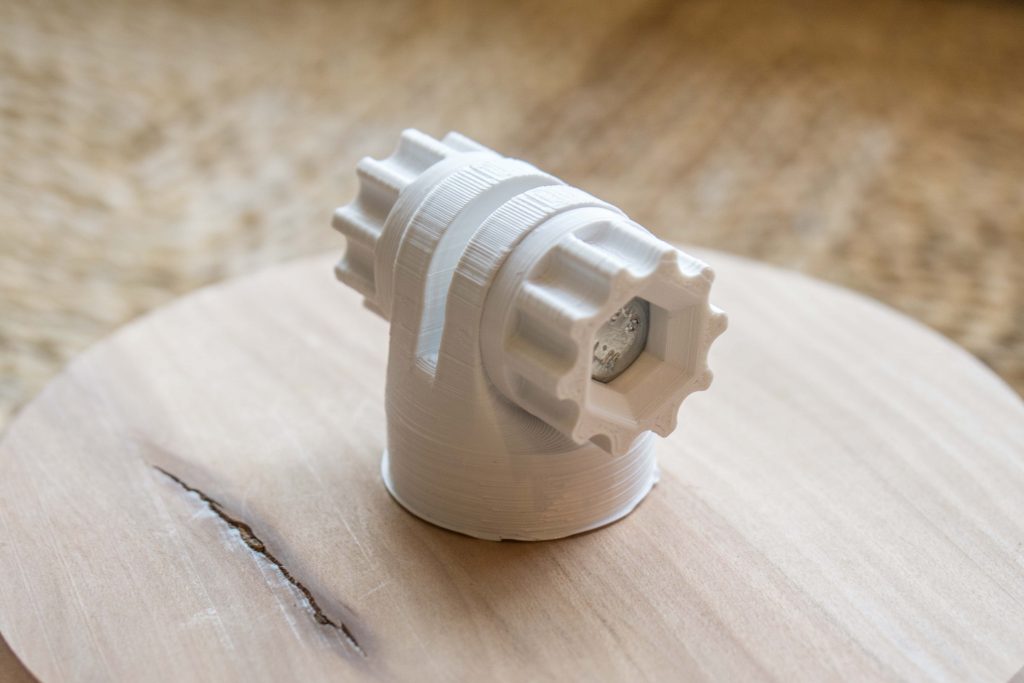
The arms should be made out of aluminium and I found some nice bars I can make them of. The first step will be to mill them out of some old wood planks I got. That is a good test to see if the dimensions of the parts work together well from a design perspective. The final arms are then milled as intended when the design is validated.
The lampshade is 3D printed and adapted to a regular E14 lamp socket. The threads came out usable on first try and I will keep those first parts.
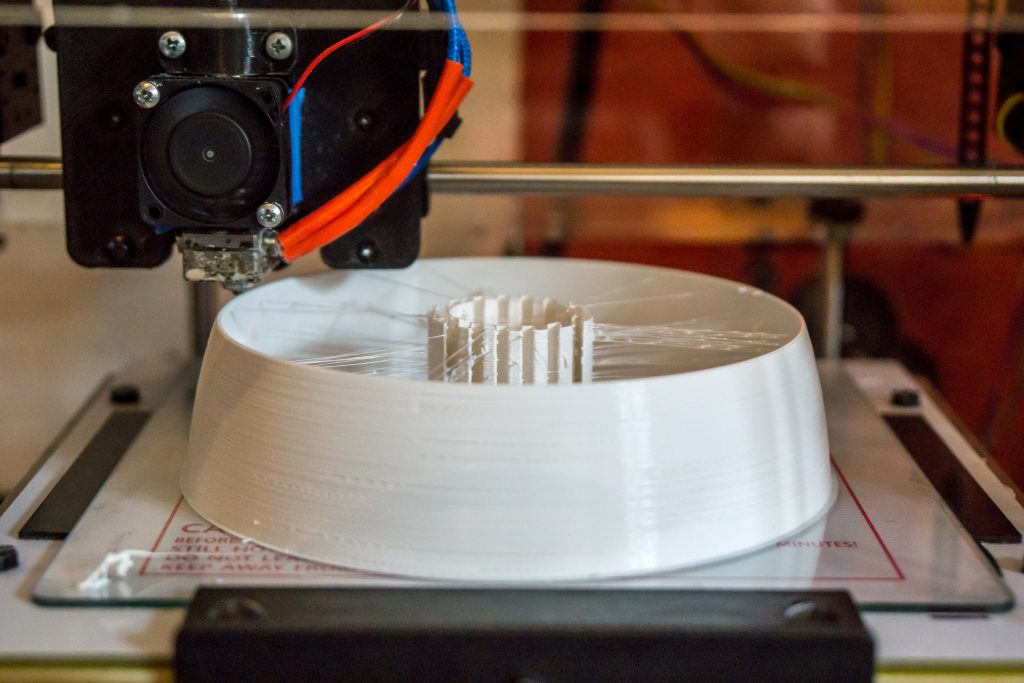
The project was started in july and was delayed because I had to build the MPCNC first but I´m almost finished by now. Pedestal and arms need to be cnced and some of the knobs are left to be printed.