I finished my C-Beam kit from Ooznest some days ago and I thought you might be interested in some of the „issues“ during the build
First of all, it has been a big pleasure to build this machine. When you´re designing things yourself most of the time there is a point where you just value a well thought out kit that just fits, as expected from a aluminum profile kit. 😛
It took roughly two afternoons to get everything together, followed up by some additonal hours of choosing the right software and adjusting the settings. Hendrik found a nice little programm called cnc.js. I had a look at the standard solutions openbuilds suggested and chllipeppr but they didn´t seemed quite right. It worked straight away and despite I haven´t tested it yet with a real cutting job I can really recommend it.
As I´m using the Kress from my MPCNC for testing purposes on the C-Beam I had to do some minor modifications to the tool clamp. I had to get it lower than the intended mounting point and all I had to do was grinding the screws a little down on the edges.
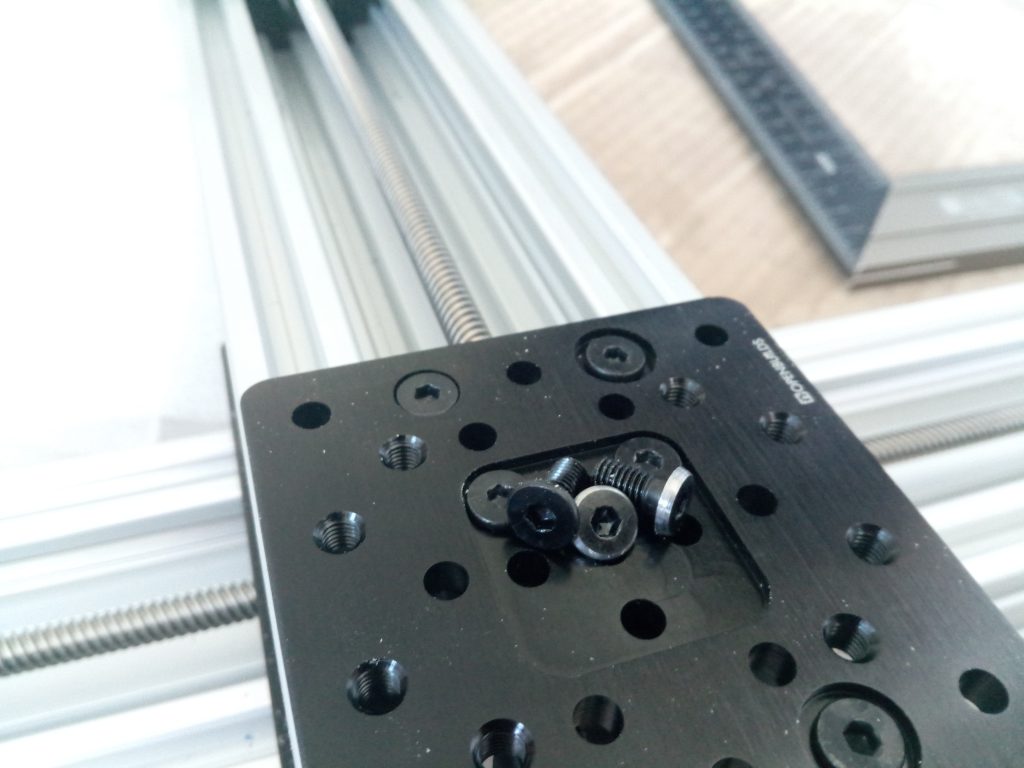
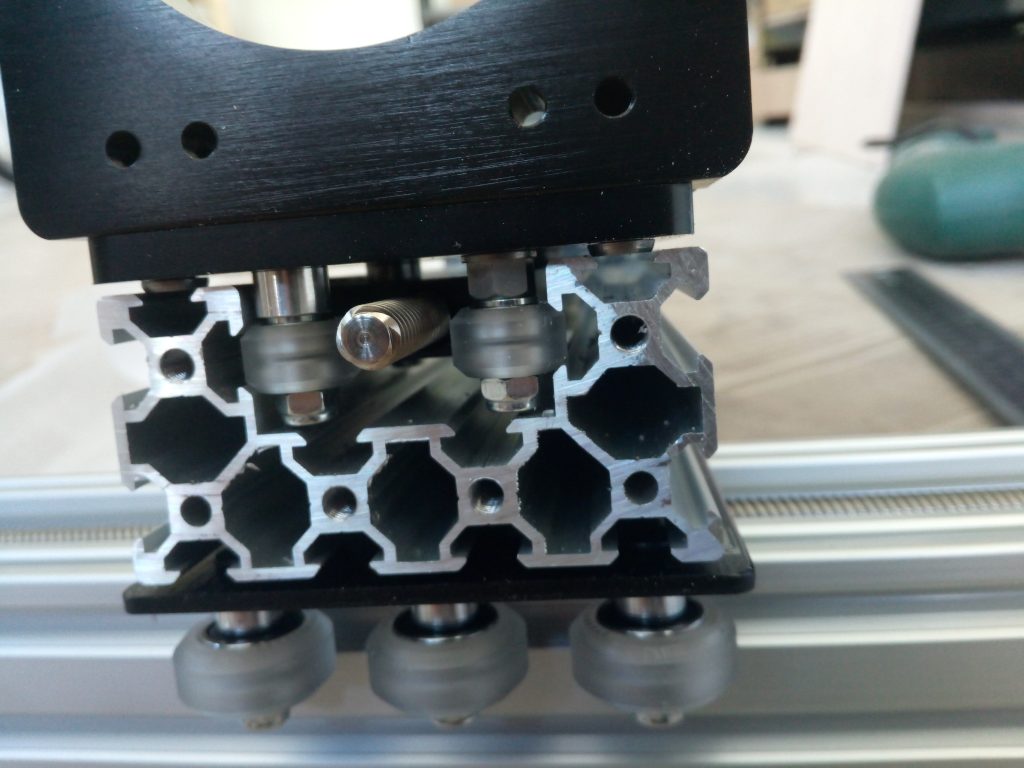
That way It was possible to screw the clamp from the backside of the plate securely. Not as good as the corners that are intended for this but it should work. At least two of them are securing the clamp from above.
What I didn´t liked so much and I suppose it´s not a common thing with the kit is the quality of the supplied cables. They were crimped on the isolation and that meant they didn´t had any reliable contact to the PSU. After three seconds the PSU switched off. My first thought was that the PSU was faulty and the second was that I might had connected something wrong. As I repeatedly check connections before I power something up I usually suspect the error elsewhere. 🙂
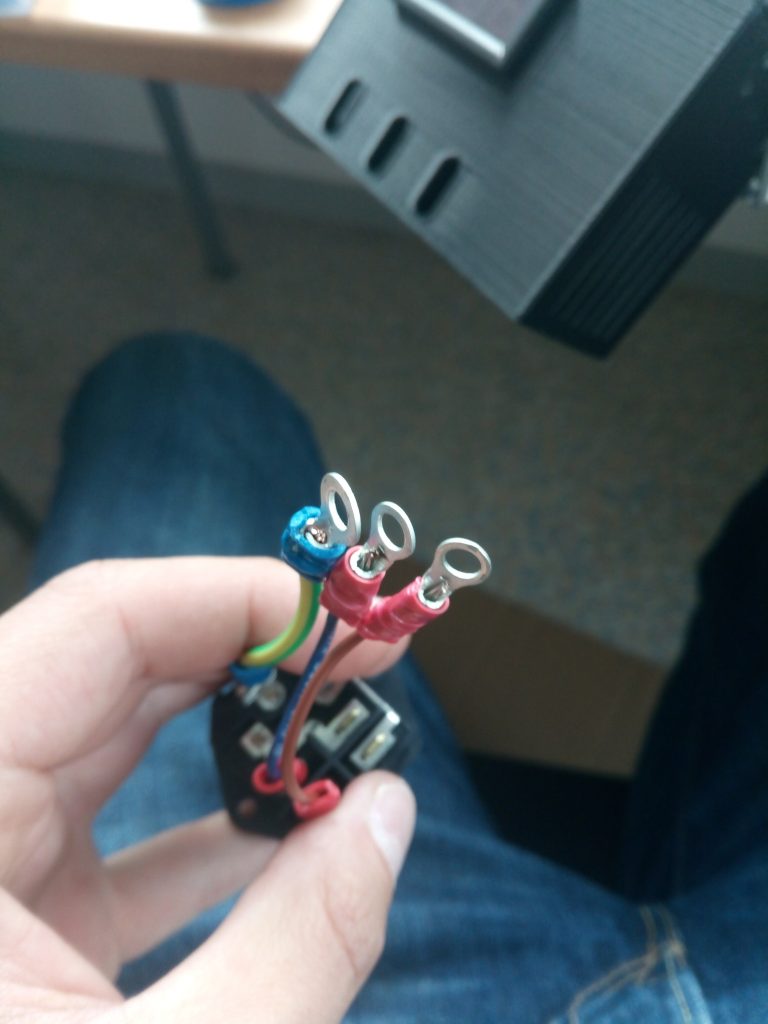

The bare metal shoudln´t stick out at the front and crimping the isolation leads to missing pressure on the cable itself causing a loose connection. I corrected this to get it stable and safe and everthing works fine now.
Those were the only two points I had to modify. Everthing else went smoothly. Pictures from the final machine will follow soon 🙂